Meaningful discussion outside of the potato gun realm. Projects, theories, current events. Non-productive discussion will be locked.
-
saladtossser
- Sergeant 3
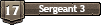
- Posts: 1234
- Joined: Sat Mar 26, 2005 10:40 am
- Location: Toronto
-
Contact:
Thu Apr 27, 2006 4:00 pm
belts and pulleys are easy to do, but cover it up so u wont get your fingers jammed in
"whoa... I thought pimpmann was black..."-pyromanic13
-
jrrdw
- Moderator
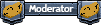

- Posts: 6572
- Joined: Wed Nov 16, 2005 5:11 pm
- Location: Maryland
- Has thanked: 39 times
- Been thanked: 22 times
-
Contact:
Thu Apr 27, 2006 4:46 pm
Looks like a swimming pool pump to me, probly 1/4 HP. Little gear on motor, big gear on machine, or just get any size gears/pulleys and set up a slipper clutch like on a rideing mower. The only problem with a clutch is you can only do lite work, plastic/soft metal, anything else will jam it up.
-
dragon finder
- Specialist 3
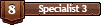
- Posts: 398
- Joined: Sun Jan 22, 2006 10:31 pm
Thu Apr 27, 2006 6:08 pm
It's a 1/8 HP 1725 rpm (found the actual rpm) thrush water cerculator(sp?) pump. hopefully it will be powerful enough. I need aproximate pully diameters to get around 30 rpm Ihave no idea what the formula is. I have looked aroungd and come up with car gear ratios and not what I need (grrrrrr).
-
Atlantis
- Corporal 5
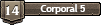
- Posts: 955
- Joined: Sat Sep 03, 2005 10:26 pm
- Location: Florida
Thu Apr 27, 2006 9:26 pm
Radius Drive Wheel/Radius Other Wheel. I think.
"There isn't a problem in the world that can't be solved by the proper application of explosives"
-
jrrdw
- Moderator
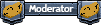

- Posts: 6572
- Joined: Wed Nov 16, 2005 5:11 pm
- Location: Maryland
- Has thanked: 39 times
- Been thanked: 22 times
-
Contact:
Fri Apr 28, 2006 6:17 am
If you double the size of the motor shaft, that will half the rpm's, so on and so on. Figure the machine the same way, do the math so the machine starts the same size as the motor shaft, then go from there, know what i mean? Write it all down from the get go so you don't get confused, it works for me when i have to do this sort of thing. Let me know how it works out for you. Maby even set up you math problems in out line from so labeling them will be easier.
-
boilingleadbath
- Staff Sergeant 2
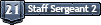
- Posts: 1635
- Joined: Sat Mar 12, 2005 10:35 pm
- Location: Pennsylvania, USA
Sat May 06, 2006 4:13 pm
I beleive that with syncronous motors, the (in this case) 1725 rpm is it's rpm at rated load. With a ball mill - not a very hefty load - you can expect it to be much closer to 1800 rpm... not that that 5% really matters much, just pointing it out.
-
dragon finder
- Specialist 3
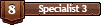
- Posts: 398
- Joined: Sun Jan 22, 2006 10:31 pm
Sat May 06, 2006 9:44 pm
well the motor will have a 2" pully on it that will turn a 4" pully that turns a 1/2" rod that turns a 5 gallon bucket......sounds like it would give me around what i need.
UPDATE: May 13, 2005
i have the motor all hooked up and ready to use as soo as the frame is ready for the ball mill.
(i had to get the emergency cover and thats 300V wire^.=.^)
