Is it possible to weld together steel and aluminum?
EDIT:
Maybe two questions in one topic...
How sturdy is structural steel tubing? 2" diameter
steel and aluminum
- sergeantspud2
- Specialist 3
- Posts: 315
- Joined: Tue Jun 07, 2005 5:43 pm
- Location: So Cal


4.If you have enough grease & a big enough hammer, you can put anything... anywhere
3.If all else fails, hit it with a big hammer
2.Matter will be damaged in direct proportion to its value
1.If anything simply cannot go wrong, it will anyway
- sergeantspud2
- Specialist 3
- Posts: 315
- Joined: Tue Jun 07, 2005 5:43 pm
- Location: So Cal
I have a scuba tank that I making into a future cannon, is it even possible to weld the aluminum on the tank to an aluminum pipe? The aluminum on the tank is VERY dense (or maybe it just seemed like it becuase it was soo thick) will that make it harder to weld?
And by sturdyness in structural steel i mean pressure handling
And by sturdyness in structural steel i mean pressure handling


4.If you have enough grease & a big enough hammer, you can put anything... anywhere
3.If all else fails, hit it with a big hammer
2.Matter will be damaged in direct proportion to its value
1.If anything simply cannot go wrong, it will anyway
- Fnord
- First Sergeant 2
- Posts: 2239
- Joined: Tue Feb 13, 2007 9:20 pm
- Location: Pripyat
- Been thanked: 1 time
- Contact:
Scuba tanks are good for around 3000 psi.
Aluminum doesn't really vary in density. Tanks are usually at least 1/4" thick, but you won't have trouble welding it.
If I were you, I'd just weld on a threaded adaptor and make the rest of the gun out of steel (or pvc).
Aluminum doesn't really vary in density. Tanks are usually at least 1/4" thick, but you won't have trouble welding it.
If I were you, I'd just weld on a threaded adaptor and make the rest of the gun out of steel (or pvc).
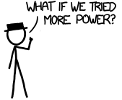
Well you first need a machine that can weld aluminium ( in AC). That would be expensive if you didn't have one now, and could be expensive to have someone do it for you.
It wouldn't be essentially harder to weld, because you just turn your amprege up but the weld may not penetrate causing a weak weld. With two different thincknesses of aluminium though, it is easy to "blow away" the thinner piece. Meaning that a hole is create due to a lot of heat (your amprege needed for the thicker stuff) on the thinner side.
I would take advice from fnord, sounds like a much easier and affordable idea.
It wouldn't be essentially harder to weld, because you just turn your amprege up but the weld may not penetrate causing a weak weld. With two different thincknesses of aluminium though, it is easy to "blow away" the thinner piece. Meaning that a hole is create due to a lot of heat (your amprege needed for the thicker stuff) on the thinner side.
I would take advice from fnord, sounds like a much easier and affordable idea.
- sergeantspud2
- Specialist 3
- Posts: 315
- Joined: Tue Jun 07, 2005 5:43 pm
- Location: So Cal
Yep that was my plan. Well its not actually a scuba tank, its a SCBA tank (firefighter) and no joke, the valve stem is 2" thick!_Fnord wrote:Scuba tanks are good for around 3000 psi.
Aluminum doesn't really vary in density. Tanks are usually at least 1/4" thick, but you won't have trouble welding it.
If I were you, I'd just weld on a threaded adaptor and make the rest of the gun out of steel (or pvc).
I have a friend that can weld but im not sure what kind of welding he does... so I guess Ill have to ask him
Thanks


4.If you have enough grease & a big enough hammer, you can put anything... anywhere
3.If all else fails, hit it with a big hammer
2.Matter will be damaged in direct proportion to its value
1.If anything simply cannot go wrong, it will anyway
- rna_duelers
- Staff Sergeant 3
- Posts: 1739
- Joined: Mon Sep 26, 2005 7:07 am
- Location: G-land Australia
This is something I ran into when I started my hybrid,I would go with welding something like I was going to onto it,as it is thick and made of aluminium but get a quality one!Mine was poor quality and the threads ripped off the pieces when I tested it on another fitting.
The piece was a aluminium Cam lock,I cut the lip off it and was going to get the end of the camber machined out and have it welded into place for my hybrid,but it f***** up on me and I haven't been motivated to start my hybrid over again.
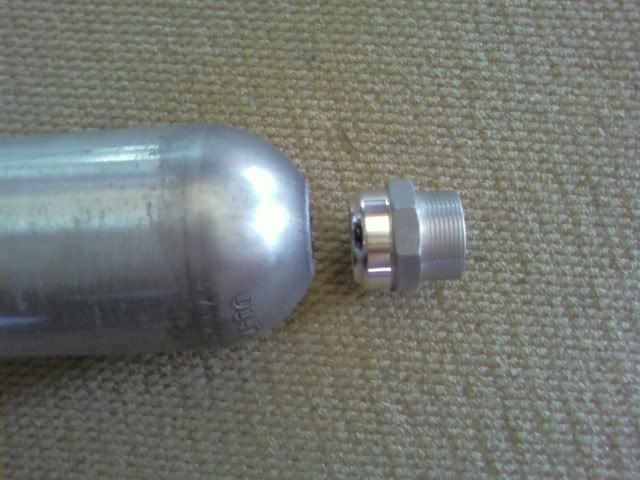
The piece was a aluminium Cam lock,I cut the lip off it and was going to get the end of the camber machined out and have it welded into place for my hybrid,but it f***** up on me and I haven't been motivated to start my hybrid over again.
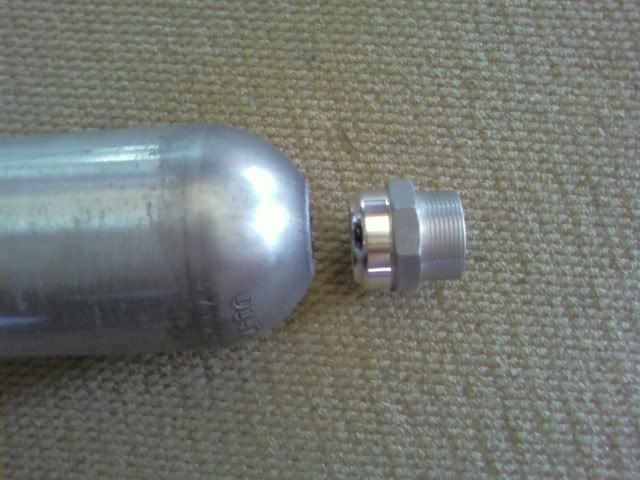
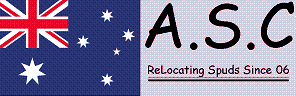
- frankrede
- Sergeant Major 2
- Posts: 3220
- Joined: Thu Jul 20, 2006 9:47 pm
- Has thanked: 1 time
- Been thanked: 1 time
The polarity is irrelevant in this case.octane89 wrote:No. To weld steel you use DCEN (direct current electrode negative) and to weld aluminium you use AC (Alt. Current).
Im a certified welder (for structure steel)in four different types of welding, so I think you can take my word.
You can weld steel in DCEN, DCEP, or AC.
The reason the can't be welded together is because the quite simply are two different types of metal and the filler metal just won't work.
The only time I have welded two different types of metal is steel and stainless together.
Current project: Afghanistan deployment