I was talking in terms of the traditional multi-stage driven piston LGGramses wrote:not so; CLGGs are relatively simple and not disposable. They're basically hybrids.inonickname wrote:An effective light gas gun and parts that aren't complex, expensive and need replacing are absolutely and completely mutually exclusive.jhalek90 wrote: :tard:
The concept of a LGG has always appealed to me.
the only issue i see is crafting a design that can be used more than once, with out the need for replacing expensive parts.
"implosion" launcher
- inonickname
- First Sergeant 4
- Posts: 2606
- Joined: Sun Dec 07, 2008 3:27 am
PimpAssasinG wrote:no im strong but you are a fat gay mother sucker that gets raped by black man for fun
Actually, I'm working on a simple "traditional" design for one which requires replacing only a single, low tolerance plastic "tube" on every shot (and burst disks, of course). Should cut the machining time per reload to about 20 minutes, for a respectably fast and energetic design.
If you're going for 7-12km/s, extruding a plastic piston down the barrel behind the projectile is probably the only way to go for a conventional design. For those of us thinking more in the range of 3-5km/s, this is not necessary, and pistons can be almost indefinitely reusable. In fact, there are designs around at the moment (done by people with far more simulation skill than I currently possess) which reach 4km/s using a very finely tuned design where the piston is slowed to a near stop by the chamber pressure right before it hits the diameter reduction, and thus requires no disposable parts at all (save the burst disk).
If you're going for 7-12km/s, extruding a plastic piston down the barrel behind the projectile is probably the only way to go for a conventional design. For those of us thinking more in the range of 3-5km/s, this is not necessary, and pistons can be almost indefinitely reusable. In fact, there are designs around at the moment (done by people with far more simulation skill than I currently possess) which reach 4km/s using a very finely tuned design where the piston is slowed to a near stop by the chamber pressure right before it hits the diameter reduction, and thus requires no disposable parts at all (save the burst disk).
Spudfiles' resident expert on all things that sail through the air at improbable speeds, trailing an incandescent wake of ionized air, dissociated polymers and metal oxides.
- jackssmirkingrevenge
- Five Star General
- Posts: 26216
- Joined: Thu Mar 15, 2007 11:28 pm
- Has thanked: 576 times
- Been thanked: 347 times
That's quite a calculation but worth the effort.DYI wrote:In fact, there are designs around at the moment (done by people with far more simulation skill than I currently possess) which reach 4km/s using a very finely tuned design where the piston is slowed to a near stop by the chamber pressure right before it hits the diameter reduction, and thus requires no disposable parts at all (save the burst disk).
Will your design be published on these hallowed pages?
hectmarr wrote:You have to make many weapons, because this field is long and short life
I have now completed a basic 0-D two stage LGG simulation to get an idea of design parameters (for those not familiar, 0-D codes do not account for the mass of the gas, resulting in the pressure of one large body of gas being uniform anywhere inside that body at a given time). This code works similarly to GGDT, except it doesn't have a GUI, and doesn't do this:
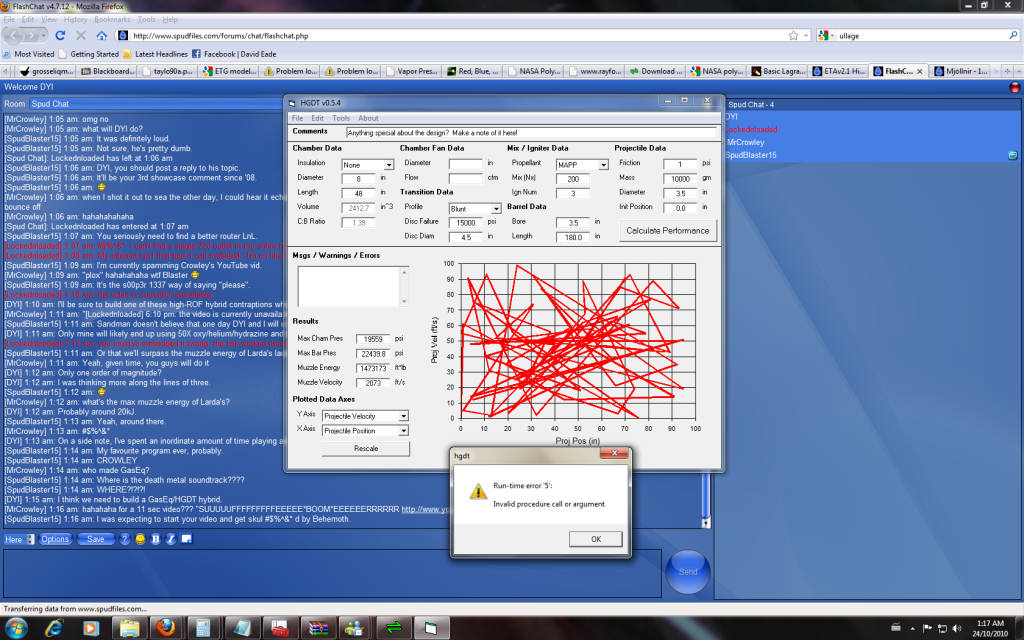
There's so much more to learn with the inclusion of double-staging. I'm having to develop a whole new intuition for gun behaviour, and there's so much more to consider that it can easily take an hour to roughly optimize a single design for a given projectile mass and diameter.
What I was trying to determine here was just how much higher the driver gas pressure could exceed the diaphragm's rupture pressure (you just can't do an 80kpsi burst disk - it's too thick). That was a success - using a 100MPa diaphragm, I can easily get the model to produce average propelling pressures of three times that (and maximum pressures over fifteen times that, if I'm not careful...).
I'm a bit short for time here and will update later, but the next step is to develop a proper 1-D code to refine the process, and possibly a 2-D CBA code for the driver gas side (more on that later).
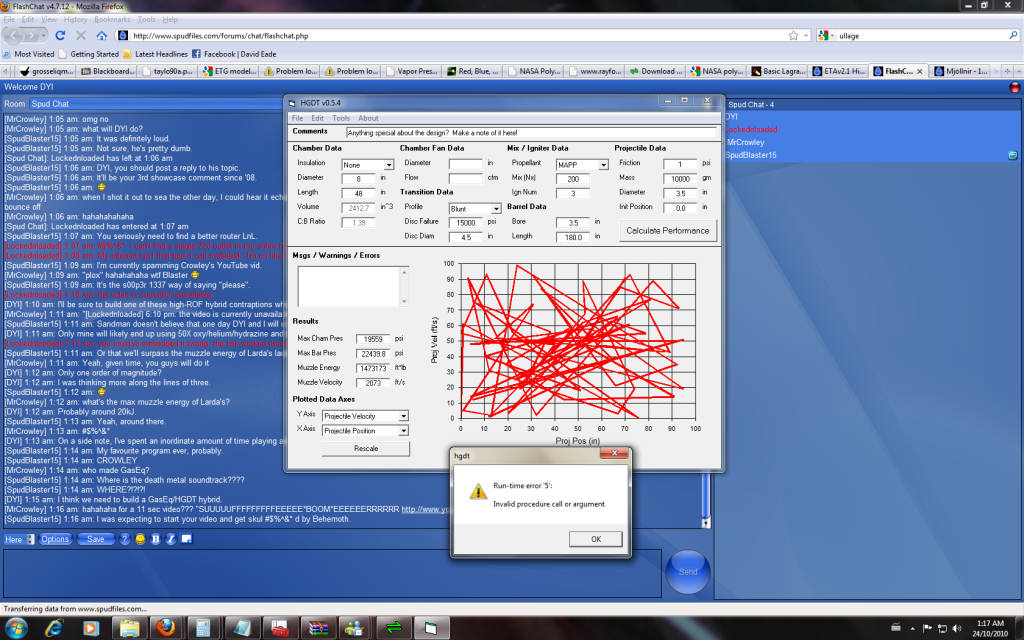
There's so much more to learn with the inclusion of double-staging. I'm having to develop a whole new intuition for gun behaviour, and there's so much more to consider that it can easily take an hour to roughly optimize a single design for a given projectile mass and diameter.
What I was trying to determine here was just how much higher the driver gas pressure could exceed the diaphragm's rupture pressure (you just can't do an 80kpsi burst disk - it's too thick). That was a success - using a 100MPa diaphragm, I can easily get the model to produce average propelling pressures of three times that (and maximum pressures over fifteen times that, if I'm not careful...).
I'm a bit short for time here and will update later, but the next step is to develop a proper 1-D code to refine the process, and possibly a 2-D CBA code for the driver gas side (more on that later).
Spudfiles' resident expert on all things that sail through the air at improbable speeds, trailing an incandescent wake of ionized air, dissociated polymers and metal oxides.
- jackssmirkingrevenge
- Five Star General
- Posts: 26216
- Joined: Thu Mar 15, 2007 11:28 pm
- Has thanked: 576 times
- Been thanked: 347 times
I hate it when HGDT does that
So... this is happening in the near future?

So... this is happening in the near future?
hectmarr wrote:You have to make many weapons, because this field is long and short life
What practical benefits would you see with a 2-D simulation over a 1-D simulation?
2-D simulation will be able to properly model heat transfer and the effects of my particular chamber geometry, but the main push to do so is the ability to use the CBA model (which doesn't really make sense in any space below ℝ<sup>2</sup>). To get an accurate high pressure equation of state tends to rely on repetitive packing density calculations using a hard sphere gas. As the CBA method models the entire simulated volume as a hard sphere gas anyway, one does away with a lot of complication (at the expense of considerably higher time complexity).
I'm pretty comfortable sticking with a quasi 1-D Lagrangian approach for the pusher gas, and the gas in front of the projectile, but given the chamber geometry and the high pressures and temperatures (and possibly shocks) encountered therein, I would not be confident in it providing sufficient accuracy in the chamber. Results of failure to model accurately could range anywhere from a misfire, to a piston extruded into the coupling and barrel (which would be quite time consuming to fix), to actual rupture of the coupling area, which would be disastrous and cost several hundred dollars to rebuild.
I'm not saying there aren't good, analytical medium-pressure EoSs for helium out there - I've seen a few in my research that fit the data quite well - but I wouldn't be comfortable relying on the results of a simulation using one with so much at stake. If some sort of modified quasi 1-D approach turns out to uniformly provide usefully accurate results I probably won't use the CBA model very much (runtimes could be a few hours), but I'll definitely be writing one.
I'm pretty comfortable sticking with a quasi 1-D Lagrangian approach for the pusher gas, and the gas in front of the projectile, but given the chamber geometry and the high pressures and temperatures (and possibly shocks) encountered therein, I would not be confident in it providing sufficient accuracy in the chamber. Results of failure to model accurately could range anywhere from a misfire, to a piston extruded into the coupling and barrel (which would be quite time consuming to fix), to actual rupture of the coupling area, which would be disastrous and cost several hundred dollars to rebuild.
I'm not saying there aren't good, analytical medium-pressure EoSs for helium out there - I've seen a few in my research that fit the data quite well - but I wouldn't be comfortable relying on the results of a simulation using one with so much at stake. If some sort of modified quasi 1-D approach turns out to uniformly provide usefully accurate results I probably won't use the CBA model very much (runtimes could be a few hours), but I'll definitely be writing one.
Spudfiles' resident expert on all things that sail through the air at improbable speeds, trailing an incandescent wake of ionized air, dissociated polymers and metal oxides.