Pressure Rating for 3 Inch Schedule 10 Aluminum Pipe
- grumpyoldman
- Specialist
- Posts: 106
- Joined: Tue Jan 31, 2012 8:04 pm
- Location: Texas
I have some 3" schedule 10 aluminum pipe. It's extruded seamless. Wall thickness is .120 inch - outside diameter is 3.5 inch. Is it safe to take it to 300 PSI? Or maybe 500 PSI? I think it would be okay up to 500 PSI but I wanted to check with you guys to make sure. Thanks!
-
- Specialist 4
- Posts: 458
- Joined: Tue Aug 02, 2011 12:31 pm
- Contact:
Yes it will be fine to 500 PSI, Make sure if you put and end cap on that it has a decent weld on it then hydro test it for pinhole leaks.
Where's my Chuck key?
- grumpyoldman
- Specialist
- Posts: 106
- Joined: Tue Jan 31, 2012 8:04 pm
- Location: Texas
Thanks Gs. Exactly what I wanted to know.
- D_Hall
- Staff Sergeant 5
- Posts: 1924
- Joined: Thu Feb 07, 2008 7:37 pm
- Location: SoCal
- Has thanked: 8 times
- Been thanked: 44 times
Stress = Load / Area
= pi * Diam * Pressure / (2*wall)
= 3.14 * 3.5 * 300 / (2 * .12)
= 13700 psi.
Depending upon the alloy & heat treatment, aluminum begins to yield at about 20,000 psi or on the order of 40,000 psi with some decent stuff giving you a safety margin of anywhere between 1.5:1 to 3:1 depending on exactly what you've got. Personal opinion is that you shouldn't do ANYTHING involving high pressure gases with less than 3:1 safety margin....
So.... If you want my opinion?
No, it's not safe.
= pi * Diam * Pressure / (2*wall)
= 3.14 * 3.5 * 300 / (2 * .12)
= 13700 psi.
Depending upon the alloy & heat treatment, aluminum begins to yield at about 20,000 psi or on the order of 40,000 psi with some decent stuff giving you a safety margin of anywhere between 1.5:1 to 3:1 depending on exactly what you've got. Personal opinion is that you shouldn't do ANYTHING involving high pressure gases with less than 3:1 safety margin....
So.... If you want my opinion?
No, it's not safe.
- jackssmirkingrevenge
- Five Star General
- Posts: 26216
- Joined: Thu Mar 15, 2007 11:28 pm
- Has thanked: 576 times
- Been thanked: 347 times
That's pretty large tubing, in general you would prefer a longer length of smaller diameter tubing. Having said that in this situation I would suspect that the end caps would blow off long before the pipe itself would fail.
hectmarr wrote:You have to make many weapons, because this field is long and short life
- grumpyoldman
- Specialist
- Posts: 106
- Joined: Tue Jan 31, 2012 8:04 pm
- Location: Texas
Hey Jack. It's a large chamber because the gun will have a large bore and I want the projectile to go very farjackssmirkingrevenge
That's pretty large tubing,


Actually, I do think it's getting close to where I want it. Maybe in another month or two I'll have a prototype put together. I still need to get a milling machine which should arrive next week. Then the real experimenting will begin. (maniacal laughter inserted here.)
Thanks D_Hall for the math lesson. The pipe is 6063-T6 with a yield of 25,000 PSI, so it would be close to a 2:1 safety margin.D_Hall
Depending upon the alloy & heat treatment, aluminum begins to yield at about 20,000 psi or on the order of 40,000 psi with some decent stuff giving you a safety margin of anywhere between 1.5:1 to 3:1 depending on exactly what you've got. Personal opinion is that you shouldn't do ANYTHING involving high pressure gases with less than 3:1 safety margin....
Since the t-shirt launcher I'm designing will be commercial, I would like at least a 3:1 safety margin on the integrity of the pressure chamber. So, if my math is right, going to a .25 wall would easily do the trick.
The tube I'll use will be 3-1/2" O.D. with a .25 wall, 6061-T6511 seamless extruded (ASTM B241) which has a minimum yield of 40,000 PSI. This info was from McMaster-Carr on their aluminum tubes. So...
S = 3.14 * 3.5 * 300 / (2 * .25)
S = 6594 PSI.
Min. Yield for 6061-T6511 = 40,000 PSI.
If my math is right that would be a 6:1 safety margin. Using 500 PSI would be a 3.5:1 safety margin. I hope you'll correct me if I've got this all wrong.
One last thing - Merry Christmas to all!
- jackssmirkingrevenge
- Five Star General
- Posts: 26216
- Joined: Thu Mar 15, 2007 11:28 pm
- Has thanked: 576 times
- Been thanked: 347 times
Is this for the T-shirt launcher though or for something else?grumpyoldman wrote:Hey Jack. It's a large chamber because the gun will have a large bore and I want the projectile to go very far. I'm still designing the t-shirt launcher that I started at the beginning of this year. It's taking so long because the more I learn about pneumatics the more the launcher design changes. At this rate I'll never have it finished.
Machine tools are a game changer, good luck with your new toysActually, I do think it's getting close to where I want it. Maybe in another month or two I'll have a prototype put together. I still need to get a milling machine which should arrive next week. Then the real experimenting will begin. (maniacal laughter inserted here.)

hectmarr wrote:You have to make many weapons, because this field is long and short life
- grumpyoldman
- Specialist
- Posts: 106
- Joined: Tue Jan 31, 2012 8:04 pm
- Location: Texas
Yep, it's for the t-shirt launcher.jackssmirkingrevenge wrote: Is this for the T-shirt launcher though or for something else?
Thanks. Now I have to learn how to operate the new toys.jackssmirkingrevenge wrote: Machine tools are a game changer, good luck with your new toys
- jackssmirkingrevenge
- Five Star General
- Posts: 26216
- Joined: Thu Mar 15, 2007 11:28 pm
- Has thanked: 576 times
- Been thanked: 347 times
I'm sure that with a fast, high flow valve you can get decent performance with sub 300 psi pressures.grumpyoldman wrote:Yep, it's for the t-shirt launcher.
The fact is that a t-shirt is a terrible projectile, and probably increasing muzzle velocity by say 50% would give you likely less than 5% range increase.
Now if you package it in say, a soda bottle cut in half...
hectmarr wrote:You have to make many weapons, because this field is long and short life
- grumpyoldman
- Specialist
- Posts: 106
- Joined: Tue Jan 31, 2012 8:04 pm
- Location: Texas
I have been thinking of ways to package the t-shirt or come up with some type of sabot. Maybe attaching a paper cone to the front of the rolled-up shirt with a ribbon on the back end. More experimenting!jackssmirkingrevenge wrote:Now if you package it in say, a soda bottle cut in half...
- Fnord
- First Sergeant 2
- Posts: 2239
- Joined: Tue Feb 13, 2007 9:20 pm
- Location: Pripyat
- Been thanked: 1 time
- Contact:
I agree with D_hall here. Even mentally picturing myself with said pipe, testing to 500 psi, seemed a bit marginal. DYI has developed a more accurate formula for pipe burst pressure, but I'm not sure where it was posted.
If you are welding aluminum, always assume the lowest common yield strength. You'll need to anneal/heat treat the welded pipe if you want anything better.
If this is for a t-shirt cannon, why not just use it as a barrel? It would be much safer than using it to contain a constant pressure load. You can use some 1.5" steel pipe fittings for the chamber at 500psi. Welded fittings would give you a considerable safety margin.
If you are welding aluminum, always assume the lowest common yield strength. You'll need to anneal/heat treat the welded pipe if you want anything better.
If this is for a t-shirt cannon, why not just use it as a barrel? It would be much safer than using it to contain a constant pressure load. You can use some 1.5" steel pipe fittings for the chamber at 500psi. Welded fittings would give you a considerable safety margin.
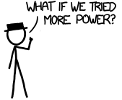
- Technician1002
- Captain
- Posts: 5189
- Joined: Sat Apr 04, 2009 11:10 am
In my testing in this field, the T shirt projectile is the limiting factor. Increasing launch speed in field tests beyond a point resulted in REDUCED range due to peeling of the outer layer of the projectile resulting in early tumble.
Here is a composite photo of a shirt launch taken with a high speed camera. The shirt from several frames is composited together to show the rapid tumble in only 5 feet of travel. We used the high speed to find out why we could not reach 400 yards with more power. The steel rule in the background was used to measure deceleration and velocity of the shirt in flight. The distortion of the leading edge of the rolled shirt is clearly a problem. Our design is online and reaches the back row of a stadium with under 50 PSI.
http://inteltrailblazerschallenge.wikispaces.com/

We had enough raw power to punch a hole in wall to wall carpet with a rolled up t shirt. More power is not the answer.

Here is a composite photo of a shirt launch taken with a high speed camera. The shirt from several frames is composited together to show the rapid tumble in only 5 feet of travel. We used the high speed to find out why we could not reach 400 yards with more power. The steel rule in the background was used to measure deceleration and velocity of the shirt in flight. The distortion of the leading edge of the rolled shirt is clearly a problem. Our design is online and reaches the back row of a stadium with under 50 PSI.
http://inteltrailblazerschallenge.wikispaces.com/

We had enough raw power to punch a hole in wall to wall carpet with a rolled up t shirt. More power is not the answer.

- D_Hall
- Staff Sergeant 5
- Posts: 1924
- Joined: Thu Feb 07, 2008 7:37 pm
- Location: SoCal
- Has thanked: 8 times
- Been thanked: 44 times
Just google "thick walled pressure vessel equation". The stuff I used is an approximation. It's pretty damned good if the wall thickness is <10% of the diameter of the pipe (and it is, in this case). The error due to the approximation won't be more than 5% or so (assuming thin walled scenario).Fnord wrote:I agree with D_hall here. Even mentally picturing myself with said pipe, testing to 500 psi, seemed a bit marginal. DYI has developed a more accurate formula for pipe burst pressure, but I'm not sure where it was posted.
But if the OP wants to use the more accurate equation, it's not hard to find.
edit: Here... Not only the equations, but an online calculator for thick walled pressure vessels... http://www.engineeringtoolbox.com/stres ... d_949.html
- grumpyoldman
- Specialist
- Posts: 106
- Joined: Tue Jan 31, 2012 8:04 pm
- Location: Texas
Thanks for the valuable info everyone. This is why I love spudfiles!